Introduction
Many large buildings and campuses have HVAC water-distribution systems, also called hydronic systems. Water is heated or cooled in a central plant, then pumped to air handlers, where ventilation air is conditioned as needed.
Maintaining and optimizing the performance of pumps and valves-the key mechanical components of water-distribution systems-can be challenging. These systems often have hidden performance problems that waste energy and cause excessive wear on equipment.
As with other mechanical components of the HVAC system, a preventive and predictive maintenance plan is an excellent way to maintain an efficient system, save energy dollars, prevent costly breakdowns, and extend equipment life.
Learn more about establishing a Best Practice Operation-and-Maintenance Program.
Types of Water Distribution Systems
Water-distribution systems are either closed-loop (cooling- or heating-system water does not come in contact with outside air) or open-loop (condenser water is exposed to outside air, usually in the cooling tower). Water in a closed loop requires less treatment than water in an open system.
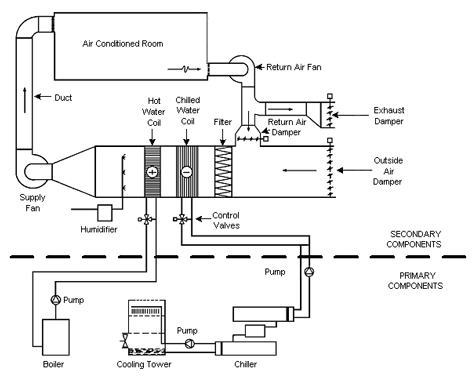
Distribution systems for chilled water and heating water
Hydronic System Types
Chilled water: Chilled-water distribution systems transport water used for air conditioning from the chiller to the air handlers, where the chilled water flows through coils in the ventilation air stream. Chilled water can also flow directly to terminal units located in the occupied space. Another variation is radiant cooling or chilled beams where chilled water flows through a radiant cooling device. Passive chilled beams provide cooling separate from the ventilation-air system. Active chilled beams are integrated into a ventilation-delivery system.
Learn more about Operation and Maintenance of Chillers.
Heating water: Heating-water systems move water from the boiler, typically located in a central plant, to air handlers or perimeter terminal units. Heating-water systems are closed loops.
Learn more about Operation and Maintenance of Boilers.
Condenser water: Condenser water loop moves water between the chiller’s condenser and the cooling tower. These systems are usually open loops.
Learn more about Operation and Maintenance of Cooling Towers.
Water-loop heat pump: This hydronic system circulates water to individual water-to-air heat pumps throughout the building. Most heating and cooling is done by individual heat pumps serving the zones in which they’re located. These heat pumps either take heat from the water loop or reject heat to the loop. In moderate weather, the water loop self-balances within a controlled range, usually 65-90°F. In hot weather, if the temperature of the loop exceeds 90°F, water in the loop will be diverted to a cooling tower. In cold weather, if the loop temperature drops below 65°F, the water will be diverted through a boiler to increase the water temperature in the loop. Hydronic heat pumps are typically closed-loop systems.
Ground-source water-loop heat pumps: This is a water-loop heat-pump system (as described above) with the addition of an extensive piping loop buried in the ground which acts as a heat sink. Heat is absorbed from the ground by the water in the piping loop in heating season, and rejected into the ground in cooling season.
Constant- and Variable-Flow Pumping Systems
All hydronic systems are either constant-flow or variable-flow. Generally, older buildings have constant-flow systems and buildings or systems built after about 1990 use some form of variable-flow control for pumping chilled and heating water.
Constant flow: A constant flow rate is maintained throughout the hydronic loop whenever the system is operating. Flow rates are established for a peak design condition, which represents a small fraction of total operating hours.
Variable flow: Variable-flow pumping can be accomplished in several ways:
- Mechanical or magnetic clutch: This type of device controls the torque to the pump from the motor in response to an external input from the DDC system, typically the differential pressure between the supply and return piping.
- Variable-speed drive: A VSD alters the frequency of the electrical input to the motor, allowing the motor to speed up or slow down as required to maintain a setpoint.
Modulating control valves: There are two valve types, two-way and three-way. Either type can be used for both constant-flow and variable-flow pumping.
- Two-way valves: These can be used in a constant-flow pumping system in conjunction with a bypass valve that controls pressure. They allow unused water to return to the central plant if the supply pressure gets too high due to a number of the valves closing. They can also be used in variable-flow pumping systems where the pump output is controlled directly by the differential pressure.
- Three-way valves: These are traditionally used in constant-flow pumping systems, where the unused water is bypassed at the coil. They are also used in variable-flow pumping systems. In special cases, several may be installed at the end of the longest piping runs. The sum of their flows equals the minimum flow the pump can produce in stably. This also allows the piping system to stay at the temperature set point in case another air handler requires immediate chilled or heating water.
Pumping System Arrangements
There are several ways to combine the above system of pumps and valves to provide energy savings as compared to a single-loop constant-flow system.
Primary-secondary variable-flow systems: Water flows through the chiller or boiler primary loop at a constant rate, and water flows through the secondary loop, which serves air handlers or fan coils, at a variable rate. The decoupled section (shown as common piping in the diagram below) isolates the two systems hydraulically. Primary-secondary variable-flow systems are more energy efficient than constant-flow systems, because they allow the secondary variable-speed pump to use only as much energy as necessary to meet the system demand.
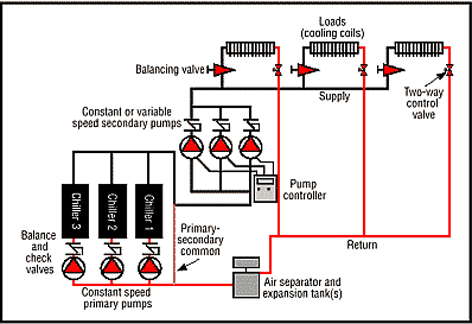
Schematic of primary-secondary loop system
Primary-loop variable-flow systems: These are chilled-water or heating-water systems with a single variable-flow loop. A two-way bypass valve is typically used to maintain a minimum specified flow rate through the chiller or boiler. Primary-loop variable-flow systems are more efficient than primary-secondary variable-flow systems.
Key Components of Water Distribution Systems
Pumps: HVAC water-distribution systems use centrifugal pumps. Centrifugal pumps have a rotating and a stationary component. The rotating section consists of an impeller and shaft; and the stationary section is the housing, which includes a casing, casing cover, and bearings. A motor spins the shaft and impeller, creating centrifugal force to increase the velocity of the water and push it through the volute (the curved funnel increasing in area) to the pump outlet.
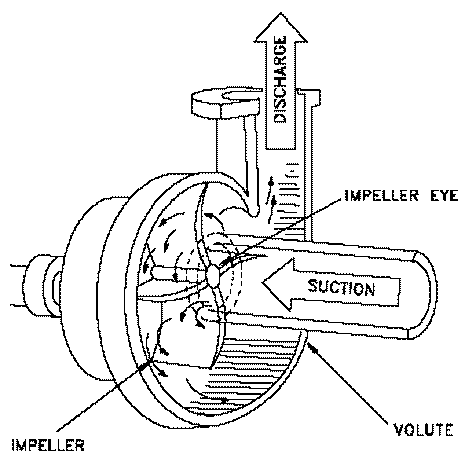
Centrifugal pump
Valves: Manual or automatic valves regulate the flow of water throughout the piping system. Valves perform four basic functions: 1) starting, stopping, and directing flow; 2) regulating or throttling flow; 3) preventing backflow; and 4) relieving or regulating pressure.
Balance valves, also called circuit setters, are a special type of regulating valve that limit flow at design conditions. This allows the system to be balanced so that every coil in the system has adequate flow. Excessive pressure drop across these valves can waste a considerable amount of energy.
Valve bodies are available in many configurations according to type of service. Regardless of function, the basic valve components are the body, seat, stem, and packing or gasket. Valve actuators control water flow through automatic valves in response to electronic or pneumatic control signals.
Either two-way or three-way valves control the flow of heating or cooling water. Two-way valves reduce flow and are commonly found in variable-flow systems. Three-way valves maintain a single flow rate by diverting the water around the coil (or other equipment such as a chiller or boiler) when necessary. Three-way valves are typically used in constant-flow systems.
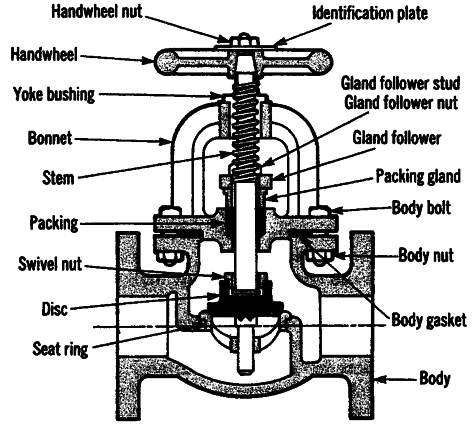
Valve components
Pipe and other system components: Pipes connect all components and, with the possible exception of hydronic-heat-pump loops, should be insulated per local codes. Other system components that need to be operated and maintained properly are expansion tanks, strainers, and gauges for pressure and temperature.
Safety Issues
Working near rotating pump shafts and couplings can be dangerous. Control panels for electrical motors and electrical connections on pump motors present a shock hazard. Heating-water systems are dangerous if not fully insulated, so be careful not to touch uninsulated piping without first checking its temperature.
Always observe lock-out and tag-out procedures during maintenance.
Best Practices for Efficient Operation
These best practices will help improve the performance of your water-distribution system and reduce operating costs:
Monitor the make-up water meter: A quick way to spot a leak in a closed-loop hydronic system is to monitor the meter on the system make-up water inlet. Reading the meter daily or weekly and comparing the readings to historical averages can help identify problems.
Investigate valve chatter: Valve chatter or water hammer coming from control valves may indicate overpressurization at the valve. High pump pressure or system imbalance can exceed the valve’s actuator shut-off rating and cause water to pass through the “closed” valve and thereby cause the chatter. Water passing through a “closed” valve causes overcooling or overheating, thereby destabilizing control and wasting energy. Generally, the shut-off pressure limit for 2-way valves with vertical actuators should be 25% greater than maximum pump head. Two-way valves with rotating actuators use a much lower torque. Three-way valves do not need as high a limit as vertical 2-way valves since they simply divert flow. Rebalancing or, as a last resort, replacing the valve actuator with one with a suitable higher pressure limit may fix the problem. Confirm the correct operating parameters of the valves in your system before making any changes.
Confirm correct control setpoints: Pumps in a variable-flow system are controlled to maintain a minimum differential pressure across the coil for a critical zone or for the coil farthest from the central plant. Make sure the differential pressure setpoint for this coil (there could be more than one) is at the proper design value. Occasionally these setpoints are raised in an attempt to fix an unrelated problem and then forgotten, wasting pump energy.
Investigate parallel pumping: Most variable-flow systems have one on-line (or lead) pump and one standby (or lag) pump. At higher flow rates, it can be more energy efficient to operate both pumps in parallel. A typical control sequence is for the lead pump to operate alone until twice its minimum flow rate is reached, then the lag pump cycles on and the two pumps operate together in parallel on the same speed-control signal. An engineering professional should determine the best strategy for your particular system.
Best Practices for Maintenance
Pumps are a vital part of HVAC and process-load applications. Pump efficiency directly affects the efficiency of other system components.
Inspect system weekly: At least once a week, a building engineer should walk the entire system and check piping, valves, and pumps for leaks and unusual noise. Noise often indicates hidden valve or pump problems. Sources of noise include turbulence, cavitation, release of entrained air, and water hammer.
Ensure adequate water treatment: Scale and sludge deposits reduce flow and impair heat transfer. An ongoing water-treatment program is critical to efficient equipment operation throughout the distribution system.
Inspect insulation: System efficiency is compromised if the distribution piping has inadequate, damaged, or wet insulation. Proper insulation can reduce radiant energy loss by as much as 90 to 95%. Removable lagging pads or snap-on insulation are available for parts such as valves that need periodic maintenance.
Test valve stroke: Test each automatic valve annually. Conduct a test where the valve actuator moves the valve stem through the entire range of the stroke. Failure to move smoothly through the entire range indicates a problem.
Maintain optimal condenser water flow: Most condenser-water systems include a strainer to remove larger material picked up in the open cooling tower. In areas with high particulate counts in the air, a side-stream mechanical filtration system is recommended to constantly filter the water and remove contaminants.
Test pump efficiency annually: Testing the efficiency of large pumps and comparing it to previous benchmarking data will help spot developing problems.
Balance or recommission the system: If temperature-control problems are found in multiple air handlers and can’t be otherwise resolved, or if the hydronic system has been expanded or modified, a test-and-balance specialist or commissioning engineer should test and recommission the system.
The table below provides a checklist for maintenance tasks.
Download this table as a Word Document
Maintenance Schedule for Water-Distribution Systems
Description | Comments | Maintenance Frequency |
---|---|---|
Check pump use/sequencing | Turn off/sequence unnecessary pumps. | Daily |
Visually inspect pumps, valves, and all mechanical joints | Visually inspect components to ensure that all equipment is operating, safety systems are in place, and no unusual leaks exist. | Weekly |
Test water | Test for proper concentrations of dissolved solids and chemistry. Adjust chemicals as necessary. | Monthly |
Check lubrication | Ensure that all bearings are lubricated according to manufacturer’s recommendations. | Monthly |
Check packing | Check packing for wear and repack as necessary. Consider replacing packing with mechanical seals. | Monthly |
Check mechanical seals | Check for leakage that exceeds the manufacturer’s specifications. Replace if necessary. | Monthly |
Motor/pump alignment | Align the pump/motor coupling to ensure efficient torque transfer to the pump. | Annually |
Check mountings | Check and secure all pump mountings. | Annually |
Check bearings | Inspect bearings and drive belts for wear. Adjust, repair, or replace as necessary. | Annually |
Check strainers | Clean strainers. | Annually |
Check expansion tanks | Inspect these tanks to make sure that the acceptance capacity is adequate and that they function properly. | Annually |
Inspect heating and cooling heat exchangers. | Temperature differences may indicate air binding, clogged strainers, or excessive scale. Determine the cause and correct. | Annually |
Cycle valves | Observe the valves moving through their full range from closed to 100% open. Back off one-half turn from 100% open to prevent the valve from “freezing” in the full open position. | Annually |
Motor condition | Check the condition of the motor through temperature or vibration analysis. | Annually |
References
ASHRAE Handbook, HVAC Systems and Equipment, 2000
US Department of Energy, Improving Pumping System Performance, Second Edition, May 2006 www1.eere.energy.gov/industry/bestpractices/pdfs/pump.pdf
Harold R. Colen, PE, HVAC Systems Evaluation, 1990
FEMP O&M Best Practices Guide 2.0, July 2004
For additional information on pumps, visit these sites sponsored by the Hydraulic Institute: www.pumplearning.org, www.pumps.org, and www.pumpsystemsmatter.org.