After learning about their unparalleled flexibility, control, and energy savings, laser manufacturing facility Novanta updated their facility to Luminaire Level Lighting Controls (LLLC). In addition to being recognized as a leader for energy efficiency, Novanta anticipates the project will result in a significant 224,996 in annual kWh savings.
Project Overview
The problem
When it came time for a lighting upgrade at their 74,000-square- foot manufacturing plant in western Washington state, Novanta—a global supplier of precision lasers for medical, industrial, and microelectronics markets—Facility Administrator Ken Packwood wanted a system that met their sustainability goals. He was also personally invested in energy efficiency because of his passion for nature conservation in the Pacific Northwest.
“I was surprised to find out that lighting was one of the top usages of energy consumption in our facility, and we also realized that some of our lighting fixtures were just outdated,” Packwood said.
He needed a financially viable lighting option for Novanta, who had been hit hard by the pandemic and overseas supply chain issues. As Packwood learned about the unparalleled flexibility, control, and energy savings of a Luminaire Level Lighting Controls (LLLC) system, he became more determined to show executives at his company that it was the right solution. He was successful in making his case, and the LLLC system has already started paying for itself.
The solution
Like so many of us do when needing to learn something new, Packwood turned to YouTube to better understand retrofitting solutions. From the videos, he quickly found he didn’t have to do the research alone. Packwood discovered other facility managers and administrators who had already been through the process. He was also approached by his local utility, Snohomish County PUD (SnoPUD) with an offer to participate in their energy conservation program. Knowing not all of their customers are lighting experts, John Petosa, Senior Program Manager at SnoPUD, provides free resources to help facility managers understand their options.
“Not all of our customers are lighting experts, and there are regional resources available that walk them through their options—free of charge. SnoPUD provides a consultant through the Trade Ally Network Northwest to help you develop and understand how our lighting retrofit program works, and your options moving forward,” said John Petosa, Senior Program Manager at SnoPUD. “We are here to help customers upgrade their lighting in their buildings, to make it more energy efficient and better for them.”
LLLC can save up to 75% in energy usage compared to standard LED fixtures, providing maximum energy savings. LLLC is also a wireless networked lighting solution that can provide flexibility for difference spaces throughout a building. This allows facility managers to automatically program lighting systems to reliably respond when occupants enter or leave a space or when there is plenty of daylight—like in an office setting.
Novanta’s lighting needs were two-fold: a solution for the office and a solution for the production plant. For Packwood, LLLC’s features made it a clear choice for lifecycle cost savings and value. But he needed to convince Novanta’s high-level executives, so he brought up the available incentives.
Local utilities including SnoPUD offer financial incentives to reduce the upfront cost of LLLC for retrofit projects, making it an even smarter investment. SnoPUD gave Novanta $87,606 and the ROI on the entire project was about five years, which aligned with the company’s capital projects requirements.
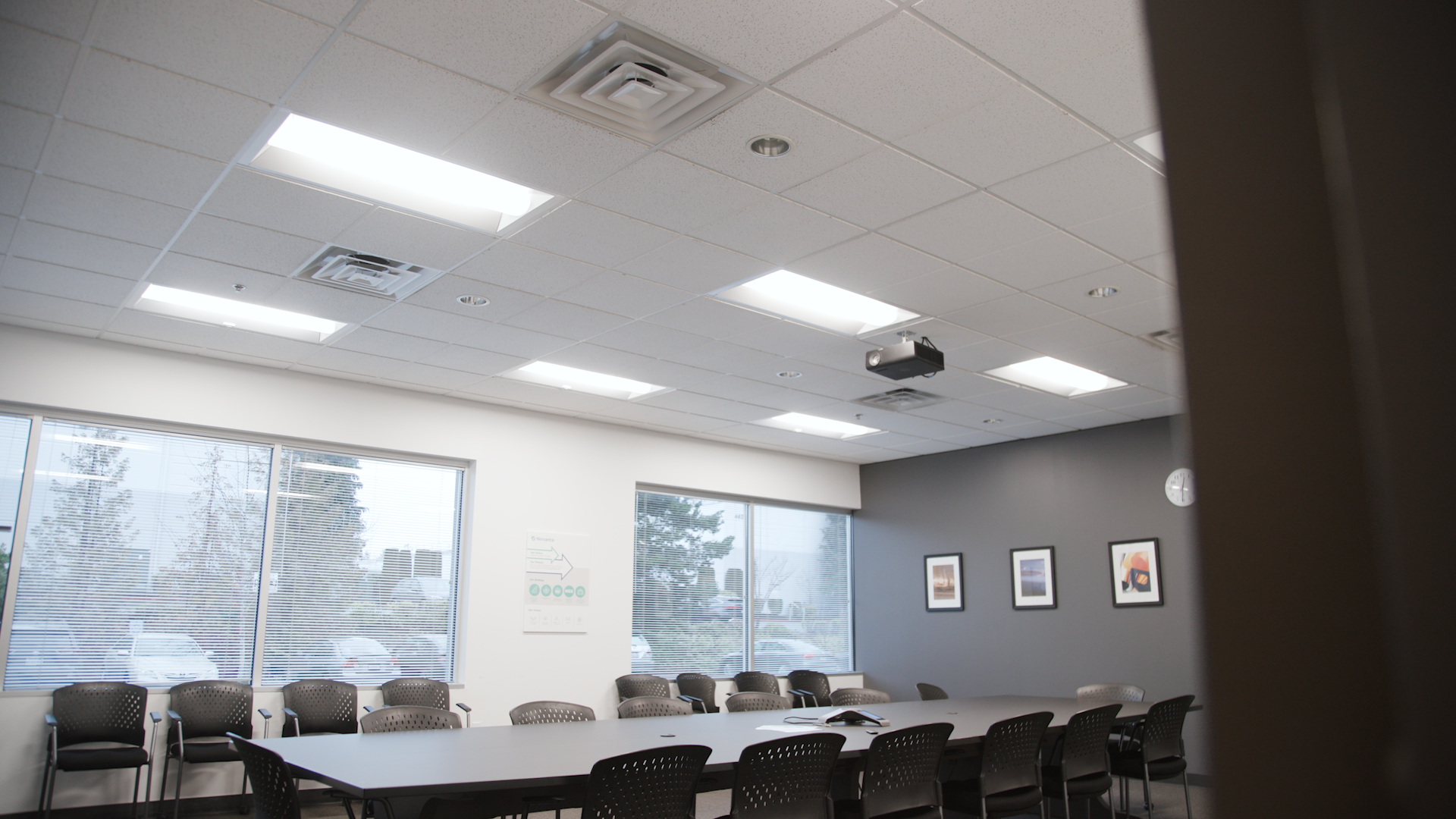
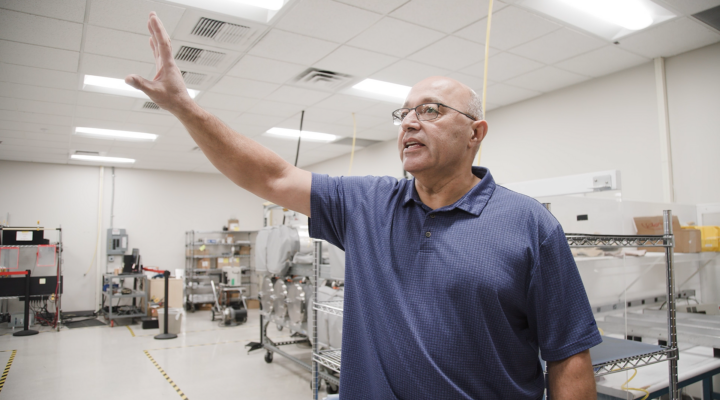
The result
Novanta’s installation was simple and took a planned, incremental approach. They put in nearly 700 fixtures between their first and second phase: 214 troffers networked via Lutron Vive in the first phase and 478 Philips EvoKit fixtures in the second phase. The flexibility of LLLC made it a perfect fit for the window-lit areas throughout the facility and met the differing needs of the office and manufacturing spaces.
As soon as the kits were installed, Packwood and his coworkers saw how LLLC was unlocking their building’s potential, especially on the manufacturing floor. Facilities like Novanta are a great use case for LLLC systems because they can be used out of the box to adapt to the needs of the building and its tenants. Specifically, facility managers can program LLLC for occupancy, trimmed to the perfect light level for employees using the equipment. This allows for lighting to respond to shift schedules or manufacturing processes that may happen in different areas of the facility at different times of the day.
“A handful of us at Novanta knew the potential, and knew what the outcome would look like, but the finished product was so much more than what we had expected,” Packwood said. “We are very happy with it. We like having level lighting throughout the facility and being able to control the level of lighting and intensity. I appreciate that I never have to change a light bulb again.”
Since adopting LLLC, Novanta has been recognized as a leader for energy efficiency, setting the bar high with an anticipated 224,996 in annual kWh savings. Packwood is proud of that accomplishment not just as a facility manager, but also as resident of the Pacific Northwest who is trying to be a good steward of its finite natural resources.
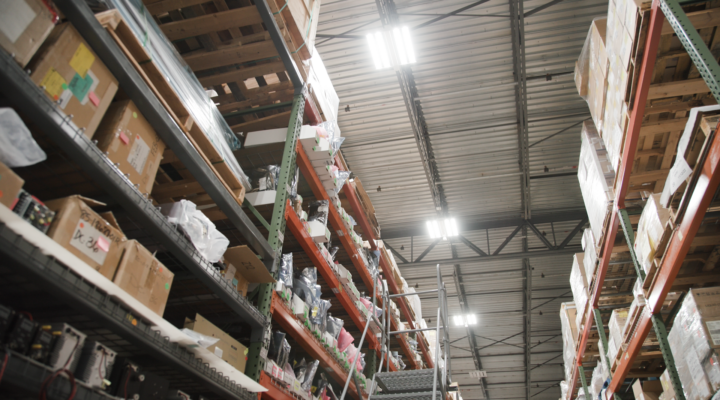
About Novanta
Located North of Seattle in Mukilteo, Washington, Novanta operates on a simple philosophy—enable new applications for sealed CO2 laser technology worldwide by engineering reliable solutions that consistently deliver precise results quickly and efficiently.
How to Get Started with LLLC
To find the LLLC system that is best for you, you’ll first need to understand the performance and business benefits that are right for your building. Contact your local utility, visit betterbricks.com/LLLC, or reach out to the Northwest Trade Ally Network for free resources to get started.