Proven energy solutions for unique energy challenges
Due to their large bays and sleeping quarters, emergency services buildings introduce unique challenges in achieving optimal comfort and energy savings. Luckily, there are many proven technologies and design solutions to overcome these challenges and enhance the energy performance of emergency service buildings.
-
Building envelope
As the building envelope rarely gets updated later in life, it’s essential to optimize its design from the start. A smart, no-cost starting point is to configure openings and overhangs for passive solar design. For instance, the building designer can prevent unwanted heat gain in the summer by situating the majority of glazing on the north and south facades, and little-to-none on the west. Similarly, using 4-foot overhangs block summer sun but allow in winter sun.
-
HVAC
Emergency stations tend to require a multi-pronged approach to HVAC with varying strategies for the sleeping quarters, the large bay and the rest of the building. Ductless mini-splits are excellent for sleeping quarters, as they provide individual control and comfort in addition to energy efficiency. So that less heat escapes through the large bay doors, bays are most efficiently heated with overhead radiant tube heaters rather than gas-fired cabinet heaters. Bays are most efficiently cooled with evaporative cooling or a large, high-volume, low-speed (HVLS) fan.
-
Lighting
As for all commercial buildings, the most cost-effective strategy is to use LED lighting to fulfill all lighting needs in an emergency station. In addition, appropriate controls such as occupancy and daylight sensors further reduce operating costs.
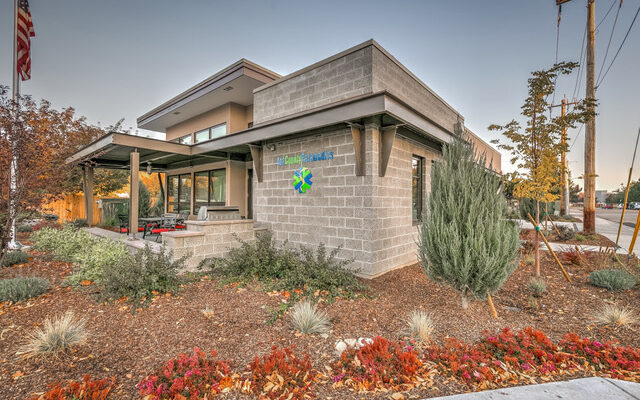
case study
The building designers, McKibben and Cooper, configured the openings and overhangs to optimize the building’s passive solar design. To reduce upfront costs, they installed gas-fired cabinet heaters in the bay as well as RTUs. For the sleeping quarters, 19-SEER-rated mini-splits were installed for their lower operating costs and individual control. For cooling the bay, they used evaporative cooling with power ventilation high-bay windows. They designed the interior and exterior lighting to be, respectively, 38% and 68% more efficient than code.
(Photo credit: EKC Construction Inc.)
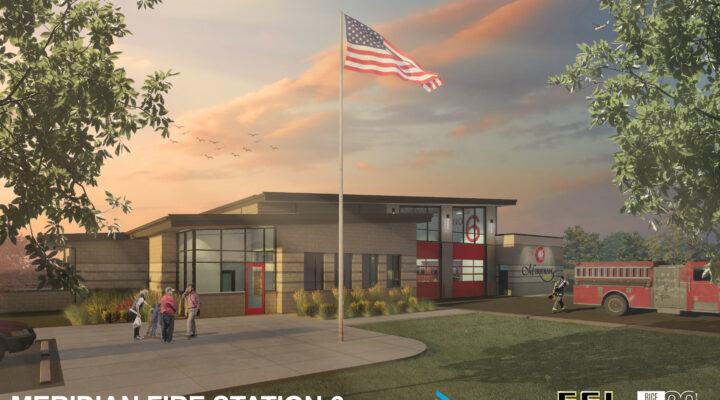
case study
With a starting goal to save money for the department and the city through energy efficiency, Pivot North designed this 10,000 sq. ft. Fire Station in South Meridian to have an envelope that performs 18% better than code. To get there, the team carefully designed the building’s solar orientation and overhangs, and incorporated a variety of energy-efficient strategies including using spray foam on the inside of structural blocks, air sealing and installing fast-acting, bi-fold bay doors. The building’s HVAC is a combination of mini-splits in five sleeping quarters and, in the bay, radiant tube heating, along with a HVLS fan and no air conditioning. They also added occupancy sensors and thermostat lockout scheduling to avoid occupants introducing inefficient thermostat settings— specifically to counteract occupants leaving the temperature very cold in the workout space.
(Photo credit: Pivot North Architecture)